【製造業】特別なシステムいらずで業務を革新
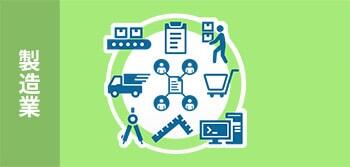
目次
受注生産のメーカーが抱える悩み
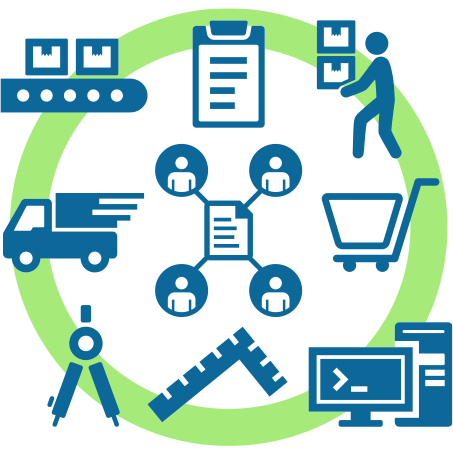
1つの製品を作り続けるような規模の大きなメーカーは、仕様や製造条件の変更はそれほど頻繁に起こらないでしょう。一方で、受注生産が多いメーカーは、製品仕様や数量・納期の変更などが頻繁に発生するのが悩みではないでしょうか。
その度に設計部門や生産管理部門は、生産本部や品質管理部門とのやり取りや調整が発生し、品質や納期を守ることに苦労されているのではないかと思います。
生産管理システムや品質管理システムなど特定業務に特化したシステムを導入する解決策もありますが、導入コストが数百万円もかかったり、多機能にも関わらず柔軟な設定や対応ができないなど、受注生産が多いメーカーから見ると費用対効果に合いません。
本稿では、特定業務に特化したシステムを用いず、
情報集約とフロー整備により、業務の「カイゼン」に成功した例をご紹介します。
ユースケース①:情報を早く確実に伝達しトラブルを未然に防ぐ
食品メーカーの例をご紹介します。
この企業は、惣菜に配合する野菜を加工している食品加工工場です。
野菜等の食材を仕入れ、顧客である惣菜工場の要求通りにカットや加工を行い、出荷しています。
扱う原料は形や品質にばらつきが大きく、加工方法もさまざまであることから、工業製品のように規格や品質を管理することが難しい状況です。
また、顧客からの要望も細かいため、顧客ごとに書類やExcelなどの表計算ソフトで規格や品質を管理していましたが、紙の書類を回送するのでは効率が悪いだけでなく、紛失やデータの保存性にも不安がありました。
問題点
- 生産業務での個別対応が頻繁に発生する
- 情報の伝達を紙やExcelで行っており、共有に時間がかかる
- 生産管理システムや品質管理システムは高額で導入できない
クラウド型のワークフローなら、これらの問題点を一気に解決できます。
ソリューション
- 1つの申請で、関係部門に同時に共有できる
- スマートフォンやタブレットでも閲覧ができ、オフィスにいなくても確認や承認可能
- 初期費用はかからず、ランニングコストも低額
ユースケース②:情報を一元管理して無駄な作業をなくす
機械メーカーの例をご紹介します。
この企業は、受注生産で機械を製造しているメーカーです。
技術営業担当者がお客様との打ち合わせをもとに設計図面を作成し、図面をもとに製造を行っています。テレワークが必要となり、図面を紙で回す方法では業務の継続が困難となり、解決できる方法を探していました。
図面管理システムも検討しましたが、現時点では機能とコストが見合っておらず導入は難しそうです。
問題点
- 図面を個別にメールやFAXで他部署に送ると、見落としが起こる
- 検図をワークフロー化したいが、柔軟な経路設計や組織変更が難しい
- 図面の保管ルールが決まっておらず、検索が困難
クラウド型のワークフローなら、これらの問題点を一気に解決できます。
ソリューション
- 紙ではなくデータで一斉に送信できる
- 担当と確認者、承認者を完全に固定しない柔軟な経路設計が可能
- 承認されたデータはクラウド上で管理が可能
スモールスタートでデジタルトランスフォーメーションへの第一歩を踏み出す
今回は、専門的なシステムを導入するまでには至らないが、現状の業務の進め方には課題が多いという企業をご紹介しました。
多くの業務にはすでに特化されたシステムが存在するのは事実です。しかしながら導入に多額の費用がかかったり、いざ導入しても従業員が使いこなせなかったりという問題もよく聞きます。
弊社が提供するクラウド型ワークフローシステムGluegent Flow(グルージェントフロー)は、専門的な知識がなくても直観的に操作できるため、導入する方にとってもユーザーにとっても使いやすいワークフローシステムです。ワークフローの導入で業務や従業員の考え方を変えて、デジタルトランスフォーメーションに取り組むきっかけとしてはいかがでしょうか。